Werkse! is exactly what we were looking for for our quality products
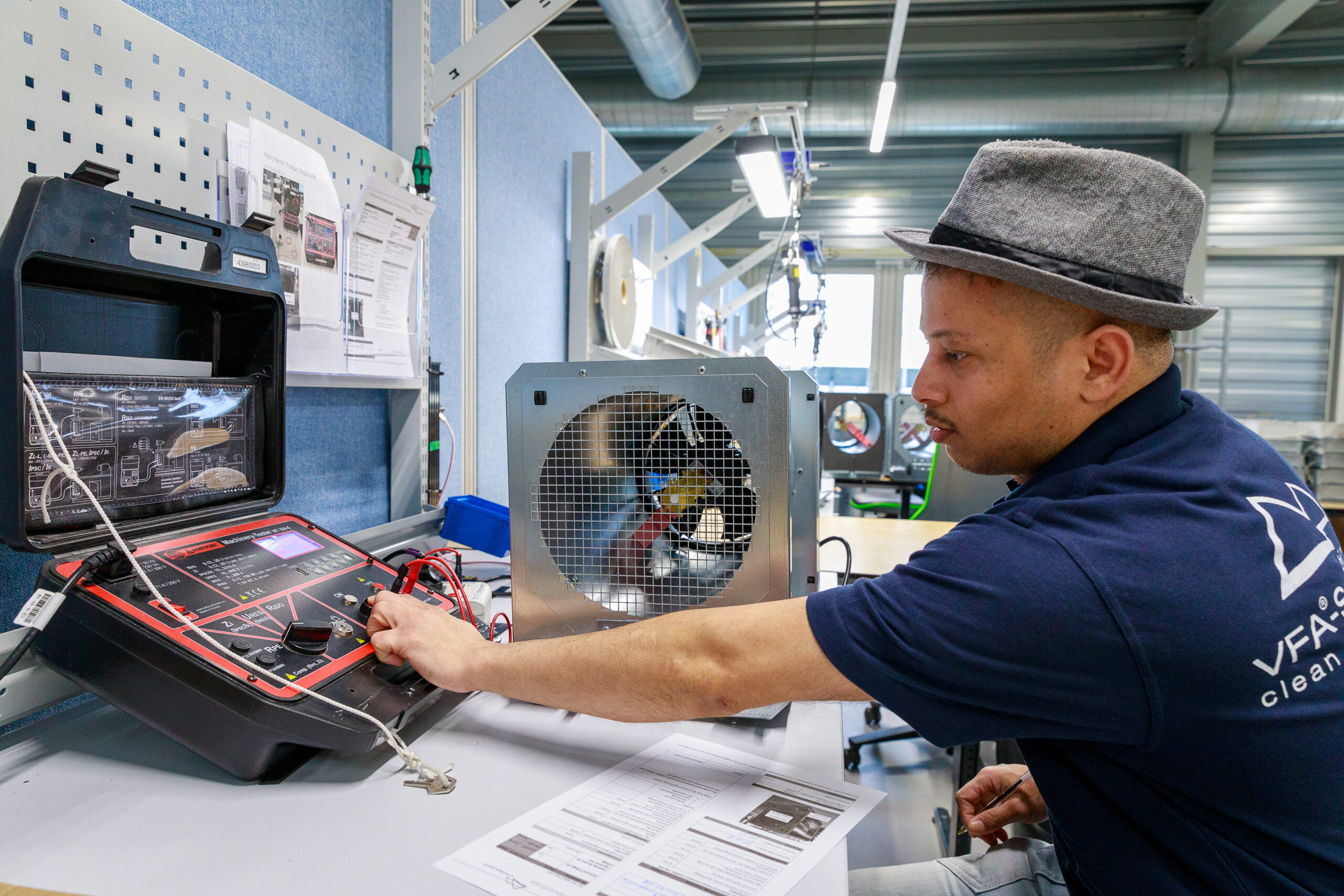
Abou VFA
VFA Solutions (VFA) is an organisation dedicated to developing clean, healthy and green technologies in the field of (indoor) air quality / Indoor Air Quality (IAQ) and filtration. VFA does this using its own patented technologies and methods. Due to growth and development, VFA was looking for a party that could take assembly and part of the process of manufacturing the products off its hands. Werkse! proved to be the right match for this.
Can you introduce yourself
Janwillem Hekman: “My name is Janwillem and I am an engineer by birth. I am now working as a consultant. Eliane Khoury, the founder of VFA, is my wife. Since its inception, I have supported Eliane at VFA with various tasks, this was mainly focused on growth and getting things right. Now I help the organisation grow further and support with e.g. drawing up contracts, negotiations with suppliers etc.”
Arno Baels: “I am Arno Baels and have been with VFA for about 15 months now. I already knew the company for some time as I am friends with Janwillem and Eliane. They had asked me to join VFA. I took the plunge and moved from Alkmaar to Rotterdam to work at VFA. I am responsible for managing production both internally and externally at Werkse!”
What challenge did VFA run into?
Janwillem: “We are a scale-up and about to become very big. We used to make all these air purifiers ourselves. And we could do that with 10 to 20 units. But now we are talking about 1,000 units and this is a different story. Also, our engineers are better at solving and designing than producing.”
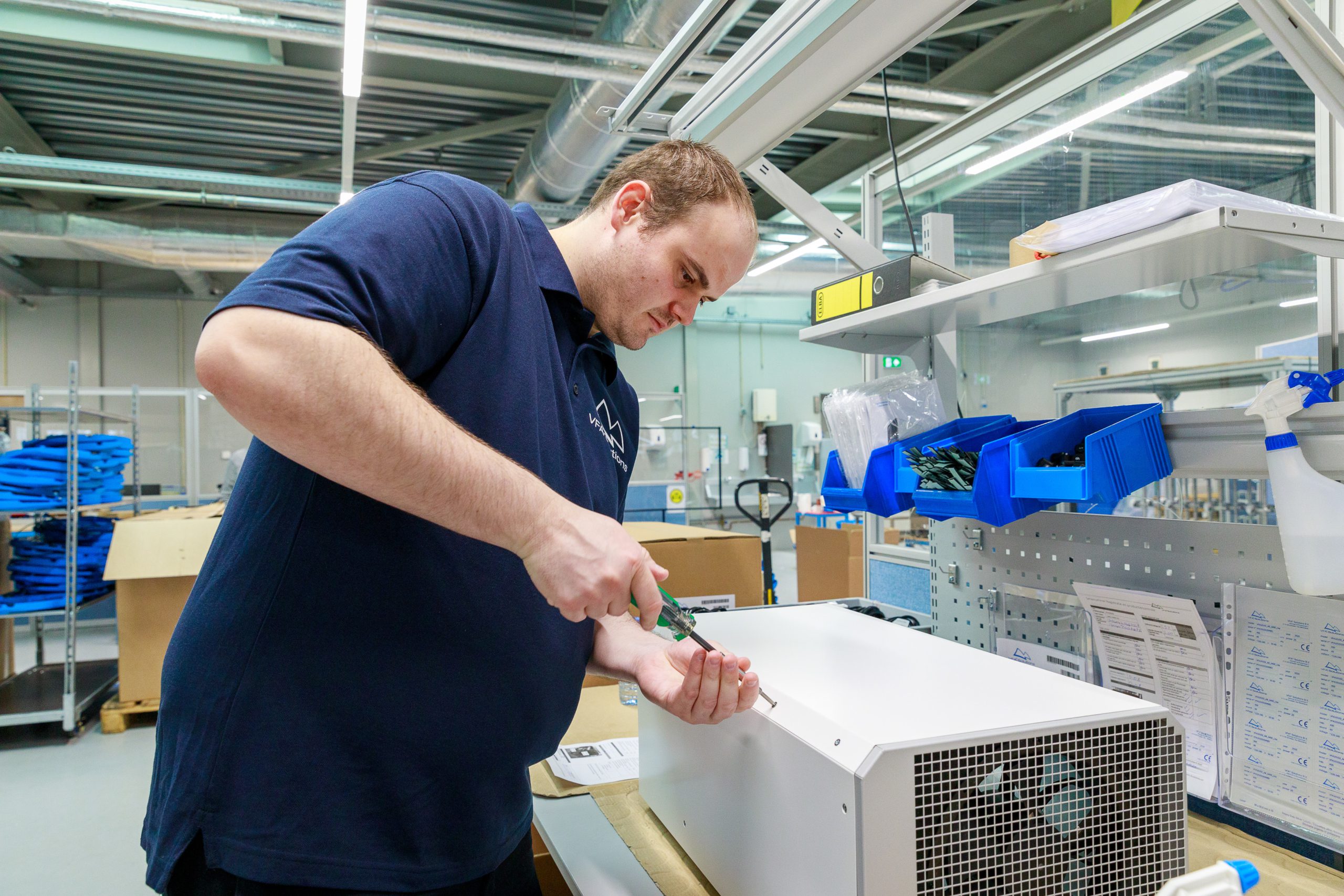
What were you looking for?
Janwillem: “We were initially looking for a local party, with a good value for money, who could help with simple assembly work. These are our stand alone products; the units you can put in the room, plug in and it does it. That recirculates; takes the air that is in the room, cleans that and sends the clean air back into the room. Other types of units you put in a ventilation duct of schools or offices, for example, to clean air from outside to inside. Later, we also added the desire to have entire products assembled and tested.”
How did you find Werkse!
Janwillem: “We were looking for a party that could help us with the assembly and got in touch with a manager at Werkse!” via via.
The rooms are bright and spacious.
What is the reason you chose to partner with Werkse
Janwillem: “The big advantage was initially that they are close by. We are in Schiedam and Delft is nearby. Werkse! has modern and easily accessible business premises and a representative appearance. The place is also always alive; there is a reception and people are conferring. The rooms where they do the assemblies are bright and spacious. We like to take our cooperation partners/customers here. In doing so, the social aspect really appeals to us. As SMEs, it is harder for us to afford to employ people who are disadvantaged. For us, this is a great way to contribute to it.”
In what ways do you cooperate with Werkse!
Arno: “Werkse! assembles part of our air cleaners. As an innovative company, our production is constantly changing. Since we want to focus on innovating our products, we are very happy to have Werkse! doing part of our production for us properly and flexibly.”
They are very strict and precise
What does assembly entail for you?
Janwillem: “We make sure Werkse! has the components. They get it delivered as a kind of kit, so to speak. Werkse! then does the assembly at its own location, where a room has been set up for our air cleaners. Here they assemble the various individual parts. And they also test whether it is then put together properly. They are very strict and precise. And that was exactly what we were looking for for our quality products.”
What training did Werkse! employees receive before they could start work
Janwillem : “We sent parts to Werkse! to assemble units with construction drawings. At the beginning, Arno went to Werkse! to instruct employees. They then randomly checked whether the units were correct according to the drawings and whether the checklist was completed. Now they do this independently and we have intensive contact for coordination.”
What does outsourcing assembly work give you
Janwillem: “We are a company that invents innovative concepts and develops them into a finished product. But we don’t necessarily want to do the production ourselves as well. We have managed to outsource a labour-intensive and repetitive part of our production. This leaves us more time for customisation processes, building prototypes and doing research. Especially at the stage VFA is in now and the current volume of units, it is an added value to scale up.”
They give tips if something is not working well.
How do you experience the cooperation with Werkse!?
Janwillem: “Pleasant, we have regular meetings about the progress of the work. Every month we sit together with the core team: three from Werkse! and three from VFA. It’s great to link up. Werkse really thinks along with you. They give tips if something doesn’t work properly during assembly. Administrative matters such as receiving invoices and issuing quotes are also handled adequately.”
In what ways is CSR central to your operations?
Janwillem: “This is an aspect we try to implement in all our work. Of course, we already supply products that contribute to human, animal and environmental health. We also strive to select all the packaging materials of our products as environmentally friendly as possible and use cardboard instead of plastic as much as possible.”
How do you see the future with Werkse! and VFA?
Janwillem: “What we do now we find nice and convenient. VFA is a technology venture, we exist when making new applications. Recently, we produced units that are also applicable for lifts. That is an example project where there is some growth. We see in that growth the possibility of putting the work down at Werkse! And that is possible for any less complex application. For both complete units, and parts of large units. It saves us space and time.”
What do you recommend to other companies
Janwillem: “We would definitely recommend Werkse! Of course it takes time to explain the assembly process properly to the workers. But after that, you know it will be fine. The work is done very well at Werkse! They work well together and are more than just a supplier of a product.”
Do you want to receive the latest news?
-
Share article
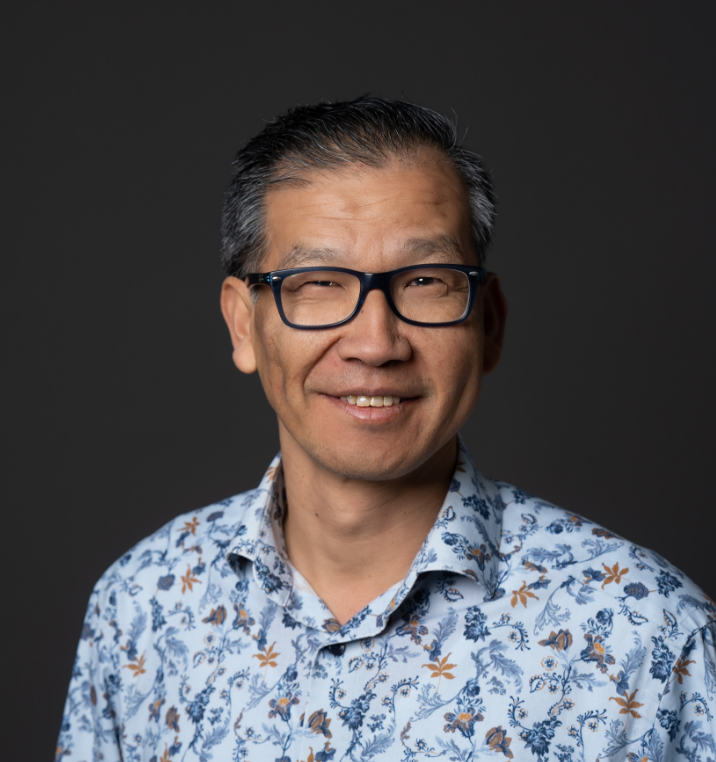